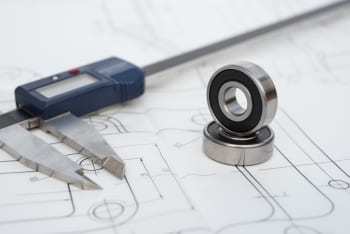
In dit artikel ga ik in op de basisprincipes van het handhaven van kwaliteit.
Het gaat hierbij om kwaliteitsborging, kwaliteitscontrole en metrologie. Kwaliteitsborging gebruiken we om vertrouwen te krijgen dat aan de kwaliteitseisen zal worden voldaan. Kwaliteitscontrole wordt gebruikt om te controleren of aan de eisen is voldaan. Dit is een subtiel verschil en in de praktijk worden de termen soms door elkaar gebruikt. Metrologie is de wetenschap van het meten. Het is de manier waarop we ervoor zorgen dat we de resultaten van metingen over de hele wereld met vertrouwen kunnen vergelijken.
Deze principes kunnen van toepassing zijn op producten of diensten, maar ik ga me concentreren op fabricage en hoe deze drie fundamentele concepten zich in die context tot elkaar verhouden. Daarom heb ik de details van specifieke methoden vermeden en ga ik niet in op de wiskunde. Dat bewaar ik voor een later artikel.
Oorsprong van de meting
De Egyptenaren gebruikten meetstandaarden, met regelmatige ijkingen, om er zeker van te zijn dat stenen in elkaar pasten in hun grote bouwprojecten. Maar moderne kwaliteitssystemen begonnen pas echt tijdens de industriële revolutie. Voor die tijd werden mechanische goederen gebouwd door ambachtslieden die elk onderdeel afzonderlijk in elkaar pasten. Dit betekende dat elke machine, en elk onderdeel daarvan, uniek was. Als een onderdeel moest worden vervangen, moest een vakman een nieuw onderdeel monteren.
Aan het eind van de 18e eeuw begonnen Franse wapenfabrikanten musketten te maken met standaard onderdelen. Dit betekende dat het leger reserve onderdelen bij zich kon dragen en deze snel kon verwisselen voor kapotte onderdelen. Deze verwisselbare onderdelen werden nog steeds in elkaar gezet om in de assemblage te passen, maar in plaats van elk onderdeel aan het individuele geweer te passen werd het aan een hoofdonderdeel gemonteerd.
Een paar jaar later begonnen Amerikaanse wapenmakers deze methode te gebruiken, maar pasten het aan aan hun ongetrainde arbeiders. Ze vijlden meters om te passen op het masteronderdeel, werknemers zouden mallen en productiemachines instellen met behulp van de meters, en ook de meters gebruiken om de onderdelen te controleren. Zo kon een rij machines, die elk één enkele bewerking uitvoerden met een ongeschoolde bediener, nauwkeurige onderdelen produceren. De onderdelen konden vervolgens snel worden geassembleerd tot complexe machines.
De basis voor moderne fabricage was dus gelegd, meer dan 100 jaar voordat Ford deze ideeën zou toepassen op een bewegende productielijn.
Kalibratie, werkelijke waarde en meetfout
Een systeem van basisonderdelen, meters en machines voor eenmalig gebruik werkte toen een heel product in één fabriek werd geproduceerd. Moderne wereldwijde toeleveringsketens hebben een ander systeem nodig.
In plaats van een fysiek hoofdonderdeel, hebben we een tekening of een digitaal CAD-model. Gespecificeerde toleranties zorgen ervoor dat de onderdelen in elkaar passen en presteren zoals bedoeld. In plaats van dat elke fabrikant naar een enkel masteronderdeel komt om zijn meters in te stellen, laten ze hun meetinstrumenten kalibreren. De instrumenten worden vervolgens gebruikt om de productiemachines in te stellen en de geproduceerde onderdelen te controleren.
Alle kwaliteit hangt af van dit ijkproces.
Het belangrijkste begrip om te begrijpen is dat alle metingen onzekerheid hebben. Als ik u zou vragen de hoogte van deze tekst te schatten, zou u kunnen zeggen: “ongeveer 4 mm”. Het gebruik van het woord “ongeveer” impliceert dat er enige onzekerheid in uw schatting zit.
In feite kunnen we nooit de exacte werkelijke waarde van iets weten, alle metingen zijn eigenlijk schattingen, en hebben een zekere onzekerheid. Het verschil tussen een meetresultaat en de werkelijke waarde is de meetfout. Omdat we de werkelijke waarde niet kunnen kennen, kunnen we ook de fout niet kennen: dit zijn onkenbare grootheden.
Alles wat wij kunnen kwantificeren over de wereld om ons heen zijn de resultaten van metingen en deze hebben altijd enige onzekerheid, zelfs als deze onzekerheid zeer klein is.
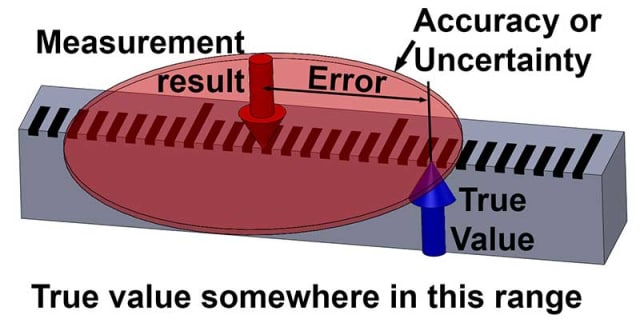
Als je de hoogte van deze tekst zou schatten als ‘ongeveer 4 mm, plus of min 1 mm’, dan heb je nu enige grenzen aan je onzekerheid gesteld. Maar u kunt er nog steeds niet 100 procent zeker van zijn dat het waar is.
Je zou een zekere mate van vertrouwen kunnen hebben, zeg 95 procent, dat het waar is. Als je de grenzen zou verhogen, tot pakweg 2 mm , dan zou je vertrouwen toenemen, misschien tot 99 procent. Dus de onzekerheid geeft enkele grenzen waarbinnen we een mate van vertrouwen hebben dat de werkelijke waarde ligt.
OK, filosofieles voorbij!
In een volgend bericht zal ik dieper ingaan op deze ideeën en hoe de onzekerheid voor een bepaald betrouwbaarheidsniveau kan worden berekend.
Onzekerheid en kwaliteit
Als we eenmaal de onzekerheid (of “nauwkeurigheid”) van een meting hebben bepaald, kunnen we deze vervolgens toepassen om te beslissen of een onderdeel aan een bepaalde tolerantie voldoet. Stel bijvoorbeeld dat een onderdeel een afmeting heeft van 100 mm +/- 1 mm. We meten het en krijgen een resultaat van 100,87 mm.
Is het onderdeel binnen de specificatie?
Het eenvoudige antwoord is: “We weten het niet, misschien wel, maar misschien zat er een fout in onze meting en is het onderdeel in werkelijkheid meer dan 101 mm. Misschien was er een nog grotere fout en is het onderdeel eigenlijk minder dan 99 mm!”
Tenzij we weten wat de onzekerheid van de meting is, hebben we geen idee hoe zeker we kunnen zijn dat het onderdeel binnen de specificatie valt. Stel dat de onzekerheid van de meting zo was gegeven dat het meetresultaat 100,87 mm +/- 0,1 mm is bij 95 procent betrouwbaarheid. Nu kunnen we met meer dan 95 procent zekerheid zeggen dat het onderdeel binnen de specificatie valt.
Dus het begrijpen en kwantificeren van de onzekerheid van metingen is van cruciaal belang voor het handhaven van kwaliteit.
Laten we nu eens kijken naar kalibratie en het bijbehorende concept van herleidbaarheid. Dit is een fundamenteel aspect van onzekerheid. Een kalibratie is een vergelijking met een referentie, en de onzekerheid van deze vergelijking moet altijd worden opgenomen, om redenen die hieronder worden uitgelegd.
Een herleidbare meting is een meting die een ononderbroken keten van ijkingen heeft die helemaal teruggaat tot de primaire standaard. In het geval van lengtemetingen is de primaire standaard de definitie van de meter; de afstand afgelegd door licht in een vacuüm in 1/299.792.458 seconden, zoals gerealiseerd door het Internationaal Bureau voor maten en gewichten (BIPM) in Parijs.
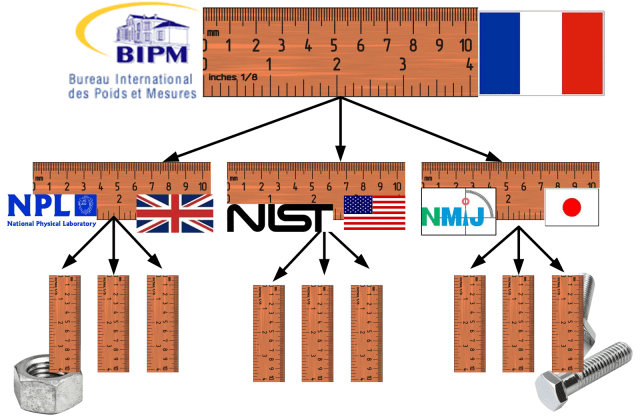
Sinds de jaren dertig van de vorige eeuw is de inch gedefinieerd als 25,4 mm en is daarom ook herleidbaar tot dezelfde meternorm. Alle metingen moeten herleidbaar zijn tot dezelfde norm om ervoor te zorgen dat in verschillende landen vervaardigde onderdelen op elkaar passen.
Onzekerheid en fout
De onzekerheid van metingen komt voort uit verschillende bronnen. Sommige daarvan zullen leiden tot een consistente fout, of vertekening, in het resultaat.
Bijvoorbeeld, de onbekende fout die aanwezig was toen een instrument werd geijkt, zal bij elk gebruik tot een consistente fout leiden. Dit type effect staat bekend als een systematische onzekerheid die leidt tot een systematische fout . Andere bronnen zullen leiden tot fouten die willekeurig veranderen telkens wanneer een meting wordt verricht.
Bijvoorbeeld, turbulentie in de lucht kan kleine, willekeurig veranderende verstoringen van lasermetingen veroorzaken, mechanische speling en uitlijning kunnen willekeurig veranderende fouten in mechanische metingen veroorzaken. Dit soort effecten staat bekend als een willekeurige onzekerheid die leidt tot een willekeurige fout .
Het is conventioneel om willekeurige onzekerheid te verdelen in herhaalbaarheid , de willekeurige onzekerheid van resultaten onder dezelfde omstandigheden, en reproduceerbaarheid , de willekeurige onzekerheid onder veranderde omstandigheden.
Natuurlijk kunnen de omstandigheden nooit precies gelijk of geheel verschillend zijn, zodat het onderscheid enigszins vaag is. De soorten omstandigheden die kunnen worden gewijzigd zijn het uitvoeren van de meting op een ander tijdstip, met een andere operator, een ander instrument, met behulp van een andere kalibratie en in een andere omgeving.
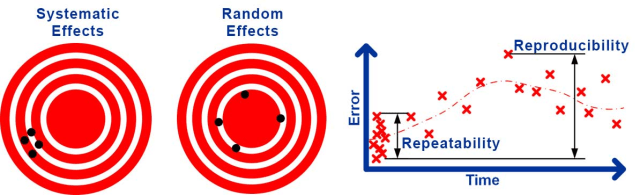
Er zijn twee veelgebruikte methoden om de onzekerheid van een meting te kwantificeren. Kalibratielaboratoria en wetenschappelijke instellingen voeren normaliter onzekerheidsbepalingen uit volgens de Guide to the Expression of Uncertainty in Measurement (GUM) .
Bij de GUM-methode worden eerst alle invloeden in aanmerking genomen die het meetresultaat kunnen beïnvloeden. Vervolgens moet een wiskundig model worden bepaald dat het meetresultaat weergeeft als functie van deze beïnvloedende grootheden. Door de onzekerheid in elke invloedsgrootheid te beschouwen en de ‘wet van voortplanting van onzekerheid’ toe te passen, kan een schatting voor de gecombineerde onzekerheid van de meting worden berekend.
De GUM-benadering wordt soms omschreven als bottom-up, omdat zij begint met een beschouwing van elke afzonderlijke invloed. Elke invloed wordt normaal gesproken opgenomen in een tabel genaamd een onzekerheidsbudget dat wordt gebruikt om de gecombineerde onzekerheid te berekenen.
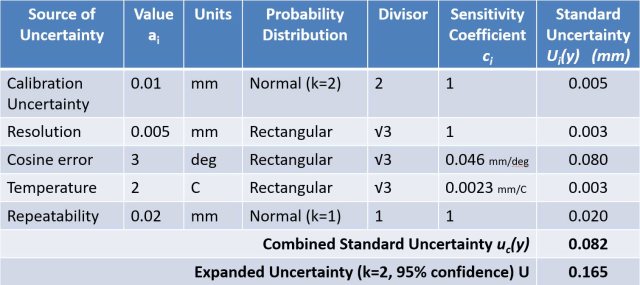
Industriële meetprocessen worden gewoonlijk geëvalueerd met behulp van een Measurement Systems Analysis (MSA)-aanpak, zoals aanbevolen binnen de Six-Sigma-methodologie, en gewoonlijk volgens de richtlijnen van de Automotive Industry Action Group (AIAG) MSA Reference Manual .
MSA omvat het uitvoeren van Gage Studies waarbij herhaalde metingen worden vergeleken met een referentie onder verschillende omstandigheden om de bias, herhaalbaarheid en soms reproduceerbaarheid te bepalen.
Een Type-1 Gage Study is de snelle controle die gewoonlijk wordt uitgevoerd om in eerste instantie inzicht te krijgen in de variatie in een meetinstrument. Het omvat een enkele operator die een enkel gekalibreerd referentieonderdeel 25 of meer keer meet en vervolgens de variatie en bias in de resultaten beschouwt. Dit type test wordt buiten MSA vaak een herhaalbaarheidsstudie genoemd.
Een onderzoek naar de herhaalbaarheid en reproduceerbaarheid (Gage R&R) wordt gebruikt om een gedetailleerder inzicht te krijgen in een meetproces. Gewoonlijk worden 10 onderdelen elk tweemaal gemeten door ten minste drie verschillende operators. Een statistische techniek, ANOVA genaamd, wordt dan gebruikt om te bepalen hoeveel variatie wordt veroorzaakt door het instrument (“gage”) en hoeveel door de operator. Hierbij worden de verandering van bediener en de daaropvolgende veranderingen in tijd en omgeving beschouwd als een volledige weergave van de reproduceerbaarheidsomstandigheden.
MSA wordt soms top-down genoemd, omdat het meetproces grotendeels als een black-box wordt behandeld en de systematische en willekeurige onzekerheden experimenteel worden bepaald. Twee belangrijke concepten in MSA zijn nauwkeurigheid , gebruikt als het equivalent van onzekerheid; en precisie , gebruikt als het equivalent van willekeurige onzekerheid.
Het voordeel van onzekerheidsevaluatie is dat alle bronnen van onzekerheid in aanmerking kunnen worden genomen en, indien goed uitgevoerd, de meest nauwkeurige schatting van de onzekerheid geeft. Problemen met deze aanpak zijn onder andere het feit dat het een metroloog vereist die in staat is om het wiskundige model te produceren en het risico van menselijke fouten die leiden tot significante invloeden die worden weggelaten of onjuist worden geschat.
De GUM-methode is ook alleen geldig voor een individuele meting die is uitgevoerd met bekende waarden voor eventuele toegepaste correcties. Het is daarom moeilijk om onzekerheidsbeoordeling correct toe te passen om de onzekerheid van een industrieel meetproces te voorspellen.
MSA kan veel gemakkelijker worden toegepast en is bedoeld om een voorspelling te doen voor de nauwkeurigheid van een industrieel meetproces. Het probleem met deze benadering is dat bepaalde systematische effecten worden genegeerd en dat reproduceerbaarheidsomstandigheden mogelijk niet volledig worden gerepresenteerd, wat leidt tot een onderschatting van de onzekerheid.
Een voorbeeld van het buiten beschouwing laten van systematische effecten is dat bij het bepalen van de bias een vergelijking wordt gemaakt met een referentie die wordt behandeld als de werkelijke waarde-in werkelijkheid heeft de referentie ook onzekerheid, die moet worden meegerekend. Deze methode berust op het variëren van alle reproduceerbaarheidsvoorwaarden, zodat de effecten daarvan zichtbaar worden in de variatie van de resultaten bij herhaalde metingen. Het is waarschijnlijk dat de wijze waarop deze voorwaarden worden gevarieerd geen volledige afspiegeling zal zijn van de variatie die tijdens het eigenlijke meetproces wordt waargenomen.
Meten en kwaliteitsborging
Tot dusver heb ik mij geconcentreerd op kwaliteitscontrole, d.w.z. hoe metingen kunnen aantonen dat onderdelen aan de specificaties voldoen nadat zij zijn geproduceerd. Laten we nu eens kort stilstaan bij kwaliteitsborging, de manier waarop we ervoor zorgen dat het proces in de eerste plaats goede onderdelen produceert.
Dit aspect van kwaliteit wordt grotendeels behandeld door Statistical Process Control (SPC) . Een proces kan worden geëvalueerd door verschillende onderdelen te maken en deze te meten om de variatie en vertekening in het fabricageproces te bepalen. In plaats van deze resultaten direct te geven, is het normaal om de tolerantie van het onderdeel te delen door de nauwkeurigheid van het proces om de Machine Capability ( C P ) of door de nauwkeurigheid van het proces om de Process Capability ( C PK ) te geven.
SPC is in veel opzichten gelijkwaardig aan MSA. Het is een top-downbenadering om willekeurige en systematische effecten te begrijpen. In plaats van metingen te evalueren, wordt het echter gebruikt om procesoutputs te evalueren. Het heeft over het algemeen dezelfde voor- en nadelen als MSA, en een bottom-up onzekerheidsbeoordeling aanpak kan worden gebruikt als deze een punt van zorg zijn.
Het kan aanvankelijk lijken dat er fundamentele verschillen zijn tussen MSA en SPC vanwege de zeer verschillende terminologie binnen SPC. Echter, variatie door gewone oorzaak (of toevallige oorzaak variatie in oudere literatuur) is het equivalent van precisie; korte termijn variabiliteit is het equivalent van herhaalbaarheid; lange termijn variabiliteit is het equivalent van reproduceerbaarheid; en speciale oorzaak variatie (of toewijsbare oorzaak variatie in oudere literatuur) is het equivalent van bias.
SPC legt ook veel meer de nadruk op het verzekeren dat een proces onder “statistische controle” staat. In grote lijnen betekent dit dat de effecten willekeurig en normaal verdeeld zijn en dat voor significante systematische effecten wordt gecorrigeerd. Dit is een sterk punt van SPC en wordt soms over het hoofd gezien bij zowel onzekerheidsbeoordeling als MSA.
Het belangrijkste instrument dat in SPC wordt gebruikt om te controleren of een proces “onder controle” is, is de controlegrafiek. Dit geeft een eenvoudig grafisch overzicht van een proces, waarbij gemakkelijk kan worden vastgesteld of een proces aan het driften is of fouten produceert die niet door normale willekeurige variaties kunnen worden verklaard. Bijvoorbeeld, als verschillende punten allemaal toe- of afnemen, zou dit erop wijzen dat het proces op drift is.
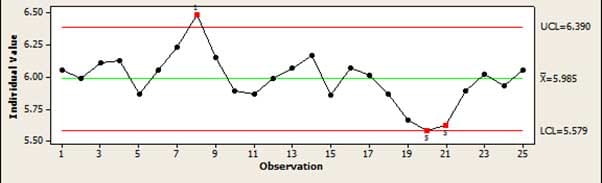
In dit artikel heb ik getracht een breed overzicht te geven van een groot en complex onderwerp. Ik heb de fundamentele principes van kwaliteitsbehoud geïntroduceerd zonder in te gaan op de wiskunde die nodig is om deze methoden toe te passen.
Blijf op de hoogte van toekomstige artikelen over deze onderwerpen.
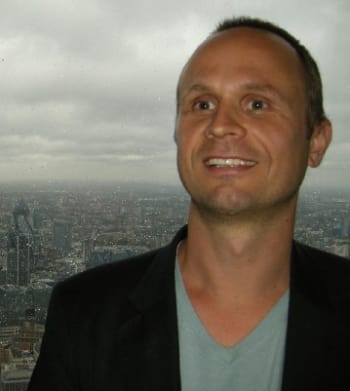
De 20-jarige ingenieursloopbaan van Dr. Jody Muelaner begon in het machineontwerp, waarbij hij aan alles werkte, van medische apparatuur tot zaagmolens. Sinds 2007 werkt hij aan de ontwikkeling van nieuwe metrologie aan de Universiteit van Bath, in nauwe samenwerking met toonaangevende lucht- en ruimtevaartbedrijven. Dit onderzoek is momenteel gericht op onzekerheidsmodellering van productiesystemen, waarbij elementen van SPC, MSA en metrologie worden samengebracht met nieuwe numerieke methoden. Hij heeft ook een interesse in fietsontwerp. Bezoek zijn website voor meer informatie.