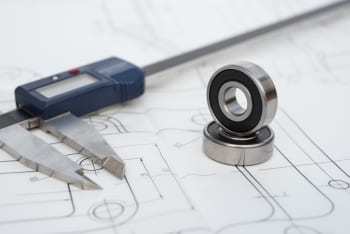
En este artículo, voy a introducir los fundamentos del mantenimiento de la calidad.
Esto implica la garantía de calidad, el control de calidad y la metrología. El aseguramiento de la calidad lo utilizamos para tener la confianza de que se cumplirán los requisitos de calidad. El control de calidad se utiliza para comprobar que los requisitos se han cumplido. Se trata de una sutil diferencia y, en la práctica, los términos se utilizan a veces indistintamente. La metrología es la ciencia de la medición. Es la forma de garantizar que podemos comparar con confianza los resultados de las mediciones realizadas en todo el mundo.
Estos principios pueden aplicarse a los productos o a los servicios, pero voy a centrarme en la fabricación y en cómo estos tres conceptos fundamentales se relacionan entre sí en ese contexto. Por lo tanto, he evitado los detalles de los métodos específicos y no me meto en ninguna de las matemáticas. Eso lo dejaré para un artículo posterior.
Orígenes de la medición
Los egipcios utilizaban estándares de medición, con calibraciones regulares, para asegurar que las piedras encajaran en sus grandes proyectos de construcción. Pero los sistemas de calidad modernos comenzaron realmente durante la revolución industrial. Antes de eso, los productos mecánicos eran construidos por artesanos que preparaban cada pieza individualmente para que encajara en un conjunto. Esto significaba que cada máquina, y cada pieza en ella, era única. Si había que sustituir una pieza, el artesano tenía que montar una nueva.
A finales del siglo XVIII, los fabricantes de armas franceses comenzaron a fabricar mosquetes con piezas estándar. Esto significaba que el ejército podía llevar piezas de repuesto y cambiarlas rápidamente por las rotas. Estas piezas intercambiables se seguían ajustando para que encajaran en el conjunto, pero en lugar de ajustar cada pieza al arma individual se ajustaba a una pieza maestra .
Unos años más tarde, los fabricantes de armas americanos empezaron a utilizar este método pero lo adaptaron para que se ajustara a sus trabajadores sin formación. Limaron los calibres para ajustarlos a la pieza maestra, los trabajadores ajustaban las plantillas y las máquinas de producción utilizando los calibres, y también utilizaban los calibres para comprobar las piezas. Esto permitía que una fila de máquinas, cada una de las cuales realizaba una única operación con un operario no cualificado, produjera piezas precisas. Las piezas podían entonces ensamblarse rápidamente en máquinas complejas.
De este modo se habían sentado las bases de la fabricación moderna, más de 100 años antes de que Ford aplicara estas ideas a una línea de producción en movimiento.
Calibración, valor real y error de medición
Un sistema de piezas maestras, calibres y máquinas de un solo uso funcionaba cuando se producía un producto completo en una sola fábrica. Las modernas cadenas de suministro globales necesitan un sistema diferente.
En lugar de tener una pieza maestra física, tenemos un dibujo o un modelo digital CAD. Las tolerancias especificadas garantizan que las piezas encajen entre sí y funcionen según lo previsto. En lugar de que cada fabricante acuda a una única pieza maestra para ajustar sus calibres, hace calibrar sus instrumentos de medición. Los instrumentos se utilizan entonces para ajustar las máquinas de producción y para comprobar las piezas producidas.
Toda la calidad depende de este proceso de calibración.
El concepto más importante que hay que entender es que todas las mediciones tienen incertidumbre. Si te pidiera que estimaras la altura de este texto, podrías decir: «es de unos 4 mm». El uso de la palabra ‘aproximadamente’ implica que hay cierta incertidumbre en tu estimación.
De hecho, nunca podemos saber el valor verdadero exacto de nada, todas las mediciones son en realidad estimaciones, y tienen cierta incertidumbre. La diferencia entre el resultado de una medición y el valor verdadero es el error de medición . Como no podemos conocer el valor verdadero, tampoco podemos conocer el error: son cantidades incognoscibles.
Todo lo que podemos cuantificar sobre el mundo que nos rodea son los resultados de las mediciones y éstas siempre tienen alguna incertidumbre, aunque ésta sea muy pequeña.
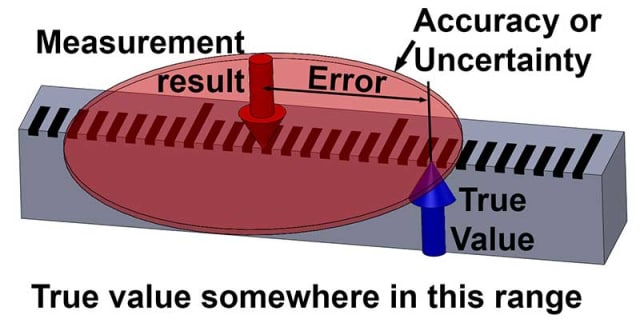
Si usted estimara la altura de este texto como ‘ alrededor de 4 mm, más o menos 1 mm’ entonces usted ha asignado ahora algunos límites a su incertidumbre. Pero todavía no puedes estar 100% seguro de que sea cierto.
Podrías tener algún nivel de confianza, digamos el 95 por ciento, de que es cierto. Si aumentas los límites, por ejemplo, 2 mm más o menos, entonces tu confianza aumentaría, quizás hasta el 99%. Así que la incertidumbre da algunos límites dentro de los cuales tenemos un nivel de confianza de que el valor verdadero se encuentra.
OK, ¡se acabó la clase de filosofía!
En un futuro post, ampliaré estas ideas y cómo se puede calcular la incertidumbre para un determinado nivel de confianza.
Incertidumbre y calidad
Una vez que hayamos determinado la incertidumbre (o «precisión») de una medición, podemos aplicarla para decidir si una pieza se ajusta a una tolerancia especificada. Por ejemplo, digamos que una pieza está especificada para medir 100 mm +/- 1 mm. La medimos y obtenemos un resultado de 100,87 mm.
¿Está la pieza dentro de la especificación?
La respuesta sencilla es: «No lo sabemos, tal vez lo esté, pero tal vez hubo un error en nuestra medición y en realidad la pieza mide más de 101 mm. Tal vez hubo un error aún mayor y las partes es en realidad menos de 99 mm!»
A menos que sepamos cuál es la incertidumbre de la medición, no tenemos ni idea de lo seguros que podemos estar de que la pieza está dentro de las especificaciones. Supongamos que la incertidumbre de la medición se dio de manera que el resultado de la medición es 100,87 mm +/- 0,1 mm con una confianza del 95 por ciento. Ahora podemos decir con más del 95 por ciento de confianza que la pieza está dentro de la especificación.
Así que entender y cuantificar la incertidumbre de las mediciones es fundamental para mantener la calidad.
Ahora, consideremos la calibración y el concepto asociado de trazabilidad. Este es un aspecto fundamental de la incertidumbre. Una calibración es una comparación con una referencia, y la incertidumbre de esta comparación debe incluirse siempre, por las razones que se explican a continuación.
Una medición trazable es aquella que tiene una cadena ininterrumpida de calibraciones que se remonta hasta el patrón primario. En el caso de las mediciones de longitud, el patrón primario es la definición del metro; la distancia recorrida por la luz en el vacío en 1/299.792.458 segundos, tal y como la realiza la Oficina Internacional de Pesos y Medidas (BIPM) de París.
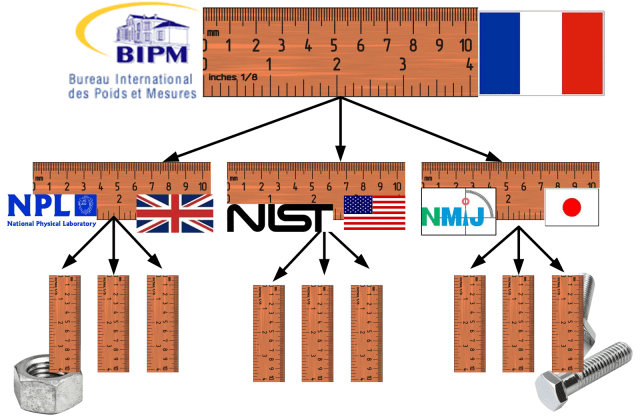
Desde la década de 1930, la pulgada se define como 25,4 mm y, por lo tanto, también es trazable al mismo patrón de metro. Todas las medidas deben ser trazables a la misma norma para garantizar que las piezas fabricadas en diferentes países encajen entre sí.
Incertidumbre y error
La incertidumbre de las mediciones surge de diferentes fuentes. Algunas de ellas conducirán a un error consistente, o sesgo, en el resultado.
Por ejemplo, el error desconocido presente cuando se calibró un instrumento conducirá a un error consistente siempre que se utilice. Este tipo de efecto se conoce como una incertidumbre sistemática que conduce a un error sistemático . Otras fuentes conducirán a errores que cambian aleatoriamente cada vez que se realiza una medición.
Por ejemplo, la turbulencia en el aire puede causar pequeñas perturbaciones que cambian al azar de las mediciones de láser, el juego mecánico y la alineación puede causar un error que cambia al azar en las mediciones mecánicas. Este tipo de efecto se conoce como una incertidumbre aleatoria que conduce a un error aleatorio .
Es convencional dividir la incertidumbre aleatoria en repetibilidad , la incertidumbre aleatoria de los resultados bajo las mismas condiciones, y reproducibilidad , la incertidumbre aleatoria bajo condiciones cambiadas.
Por supuesto, las condiciones nunca pueden ser exactamente las mismas o completamente diferentes por lo que la distinción es algo vaga. Los tipos de condiciones que podrían cambiarse son hacer la medición en un momento diferente, con un operador diferente, un instrumento diferente, utilizando una calibración diferente y en un entorno diferente.
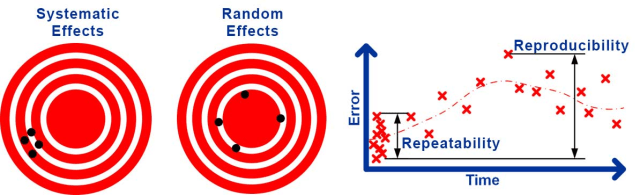
Hay dos métodos ampliamente utilizados para cuantificar la incertidumbre de una medición. Los laboratorios de calibración y las instituciones científicas suelen realizar la Evaluación de la Incertidumbre según la Guía para la Expresión de la Incertidumbre en la Medición (GUM) .
El método GUM consiste en considerar primero todas las influencias que pueden afectar al resultado de la medición. A continuación, se debe determinar un modelo matemático que dé el resultado de la medición en función de estas magnitudes de influencia. Considerando la incertidumbre en cada cantidad de entrada y aplicando la ‘ Ley de Propagación de la Incertidumbre ‘ se puede calcular una estimación de la incertidumbre combinada de la medición.
El enfoque GUM se describe a veces como ascendente, ya que comienza con una consideración de cada influencia individual. Cada influencia está normalmente listada en una tabla llamada presupuesto de incertidumbre que se utiliza para calcular la incertidumbre combinada.
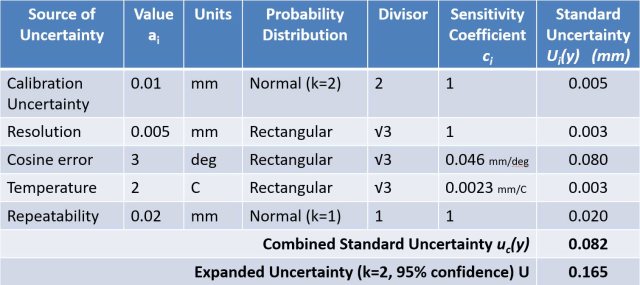
Los procesos de medición industrial se evalúan normalmente utilizando un enfoque de Análisis de Sistemas de Medición (MSA), como se recomienda dentro de la metodología Six-Sigma, y normalmente siguiendo las directrices del Manual de Referencia MSA del Grupo de Acción de la Industria Automotriz (AIAG) .
El MSA implica la realización de Estudios de Medición en los que se comparan mediciones repetidas con una referencia bajo diferentes condiciones para determinar el sesgo, la repetibilidad y a veces la reproducibilidad.
Un estudio de calibre de tipo 1 es la comprobación rápida que se realiza normalmente para comprender inicialmente la variación de un calibre. Consiste en que un solo operario mida una sola pieza de referencia calibrada 25 o más veces y luego considere la variación y el sesgo de los resultados. Este tipo de prueba suele denominarse estudio de repetibilidad fuera de MSA.
Un estudio de repetibilidad y reproducibilidad de calibres (Gage R&R) se utiliza para obtener una comprensión más detallada de un proceso de medición. Normalmente se miden 10 piezas cada una dos veces por al menos tres operadores diferentes. A continuación, se utiliza una técnica estadística denominada ANOVA para determinar cuánta variación es causada por el instrumento («calibrador») y cuánta es causada por el operario. Esto considera que el cambio de operador y los cambios posteriores en el tiempo y el entorno son una representación completa de las condiciones de reproducibilidad.
El MSA se denomina a veces top-down, ya que trata en gran medida el proceso de medición como una caja negra y determina experimentalmente las incertidumbres sistemáticas y aleatorias. Dos conceptos importantes en MSA son la exactitud , utilizada como el equivalente de la incertidumbre; y la precisión , utilizada como el equivalente de la incertidumbre aleatoria.
La ventaja de la evaluación de la incertidumbre es que es capaz de considerar todas las fuentes de incertidumbre y, si se hace correctamente, da la estimación más precisa de la incertidumbre. Los problemas de este enfoque incluyen el hecho de que requiere un metrólogo capaz de producir el modelo matemático y el riesgo de que el error humano lleve a omitir o estimar incorrectamente influencias significativas.
Además, el método GUM sólo es válido para una medición individual que se haya realizado con valores conocidos para cualquier corrección aplicada. Por lo tanto, es difícil aplicar correctamente la evaluación de la incertidumbre para predecir la incertidumbre de un proceso de medición industrial.
La evaluación de la incertidumbre (MSA) puede aplicarse mucho más fácilmente y tiene por objeto proporcionar una predicción de la precisión de un proceso de medición industrial. El problema de este enfoque es que se ignoran ciertos efectos sistemáticos y las condiciones de reproducibilidad pueden no estar totalmente representadas, lo que conduce a una subestimación de la incertidumbre.
Un ejemplo de la omisión de los efectos sistemáticos es que, al determinar el sesgo, se realiza una comparación con una referencia que se trata como el valor verdadero; en realidad, la referencia también tiene incertidumbre, que debería incluirse. Este método se basa en la variación de todas las condiciones de reproducibilidad para que sus efectos puedan verse en la variación de los resultados al realizar mediciones repetidas. Es probable que la forma en que se varíen estas condiciones no refleje completamente la variación observada durante la vida del proceso de medición real.
Medición y garantía de calidad
Hasta ahora me he centrado en el control de calidad, es decir, en cómo las mediciones pueden demostrar que las piezas se ajustan a las especificaciones una vez producidas. Ahora, consideremos brevemente el aseguramiento de la calidad, la forma en que nos aseguramos de que el proceso produce buenas piezas en primer lugar.
Este aspecto de la calidad se aborda en gran medida por el control estadístico de procesos (SPC) . Un proceso puede ser evaluado haciendo varias piezas y midiéndolas para determinar la variación y el sesgo en el proceso de fabricación. En lugar de dar estos resultados directamente, es normal dividir la tolerancia de la pieza por la precisión del proceso para dar la Capacidad de la Máquina Herramienta ( C P ) o por la precisión del proceso para dar la Capacidad del Proceso ( C PK ).
El SPC es en muchos aspectos equivalente al MSA. Adopta un enfoque descendente para comprender los efectos aleatorios y sistemáticos. Sin embargo, en lugar de evaluar las mediciones, se utiliza para evaluar las salidas del proceso. Por lo general, tiene las mismas ventajas y desventajas que el MSA, y se puede utilizar un enfoque de evaluación de la incertidumbre de abajo hacia arriba si estos son una preocupación.
Inicialmente puede parecer que hay diferencias fundamentales entre MSA y SPC debido a la muy diferente terminología dentro de SPC. Sin embargo, la variación de causa común (o variación de causa fortuita en la literatura más antigua) es el equivalente a la precisión; la variabilidad a corto plazo es el equivalente a la repetibilidad; la variabilidad a largo plazo es el equivalente a la reproducibilidad; y la variación de causa especial (o variación de causa asignable en la literatura más antigua) es el equivalente al sesgo.
El SPC también pone un énfasis mucho mayor en asegurar que un proceso está en ‘ control estadístico ‘. En términos generales, esto significa que los efectos son aleatorios y se distribuyen normalmente con cualquier efecto sistemático significativo corregido. Este es un punto fuerte del SPC y a veces se pasa por alto tanto en la evaluación de la incertidumbre como en el MSA.
La principal herramienta utilizada en SPC para comprobar un proceso ‘en control’ es el gráfico de control . Esto proporciona una visión gráfica sencilla de un proceso en la que se puede detectar fácilmente cuando un proceso está a la deriva o produce errores que no se pueden explicar por las variaciones aleatorias normales. Por ejemplo, si varios puntos aumentan o disminuyen, esto indicaría que el proceso está a la deriva.
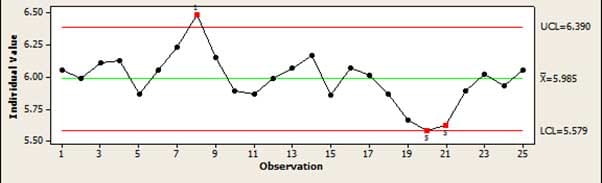
En este artículo, he tratado de dar una amplia visión de un tema amplio y complejo. He introducido los principios fundamentales del mantenimiento de la calidad sin entrar en las matemáticas necesarias para aplicar estos métodos.
Estén atentos a futuros artículos sobre estos temas.
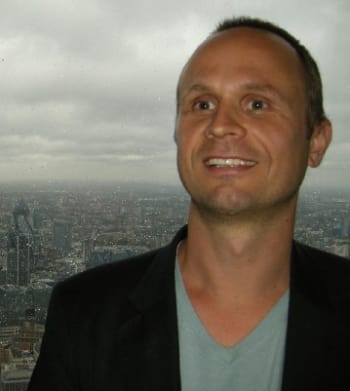
La carrera de ingeniería de 20 años del Dr. Jody Muelaner comenzó en el diseño de máquinas, trabajando en todo tipo de productos, desde dispositivos médicos hasta aserraderos. Desde 2007 ha estado desarrollando una novedosa metrología en la Universidad de Bath, colaborando estrechamente con las principales empresas aeroespaciales. Esta investigación se centra actualmente en la modelización de la incertidumbre de los sistemas de producción, reuniendo elementos de SPC, MSA y metrología con novedosos métodos numéricos. También está interesado en el diseño de bicicletas. Visite su página web para obtener más información.