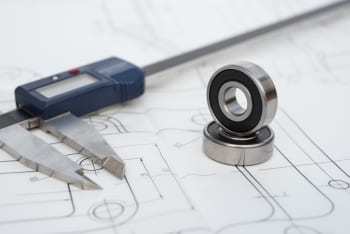
În acest articol, voi prezenta elementele de bază ale menținerii calității.
Aceasta implică asigurarea calității, controlul calității și metrologia. Folosim asigurarea calității pentru a obține încrederea că cerințele de calitate vor fi îndeplinite. Controlul calității este utilizat pentru a verifica dacă cerințele au fost îndeplinite. Aceasta este o diferență subtilă și, în practică, termenii sunt uneori utilizați interschimbabil. Metrologia este știința măsurătorilor. Este modul în care ne asigurăm că putem compara cu încredere rezultatele măsurătorilor efectuate în întreaga lume.
Aceste principii se pot aplica la produse sau la un serviciu, dar eu mă voi concentra asupra producției și asupra modului în care aceste trei concepte fundamentale se raportează între ele în acest context. Prin urmare, am evitat detaliile metodelor specifice și nu intru în niciunul dintre calculele matematice. Voi păstra asta pentru un articol ulterior.
Originile măsurării
Egiptenii foloseau standarde de măsurare, cu calibrări regulate, pentru a se asigura că pietrele se vor potrivi între ele în marile lor proiecte de construcție. Dar sistemele moderne de calitate au început cu adevărat în timpul revoluției industriale. Înainte de aceasta, bunurile mecanice erau construite de meșteri care ajustau fiecare piesă în parte pentru a se potrivi într-un ansamblu. Acest lucru însemna că fiecare mașină, și fiecare piesă din ea, era unică. Dacă o piesă trebuia să fie înlocuită, atunci un meșter trebuia să monteze o piesă nouă.
La sfârșitul secolului al XVIII-lea, producătorii francezi de arme au început să fabrice muschete cu piese standard. Acest lucru însemna că armata putea transporta piese de schimb și le putea schimba rapid pe cele stricate. Aceste piese interschimbabile erau încă aranjate pentru a se potrivi în ansamblu, dar în loc să se potrivească fiecare piesă la arma individuală, se potrivea la o piesă principală .
Câțiva ani mai târziu, producătorii americani de arme au început să folosească această metodă, dar au adaptat-o pentru a se potrivi muncitorilor lor neinstruiți. Aceștia au depus calibre pentru a se potrivi la piesa master, muncitorii reglau șabloanele și mașinile de producție folosind calibrele și, de asemenea, foloseau calibrele pentru a verifica piesele. Acest lucru a permis ca un șir de mașini, fiecare efectuând o singură operațiune cu un operator necalificat, să producă piese precise. Piesele puteau fi apoi asamblate rapid în mașini complexe.
Bazele producției moderne fuseseră astfel puse, cu peste 100 de ani înainte ca Ford să aplice aceste idei pe o linie de producție în mișcare.
Calibrarea, valoarea reală și eroarea de măsurare
Un sistem de piese de bază, calibre și mașini de unică folosință funcționa atunci când un întreg produs era produs într-o singură fabrică. Lanțurile de aprovizionare globale moderne au nevoie de un sistem diferit.
În loc să avem o piesă master fizică, avem un desen sau un model CAD digital. Toleranțele specificate asigură că piesele se vor potrivi între ele și vor funcționa conform destinației. În loc ca fiecare producător să vină la o singură piesă de bază pentru a-și regla calibrele, aceștia au instrumentele de măsură calibrate. Instrumentele sunt apoi folosite pentru a regla mașinile de producție și pentru a verifica piesele produse.
Toată calitatea depinde de acest proces de calibrare.
Cel mai important concept care trebuie înțeles este că toate măsurătorile au incertitudine. Dacă v-aș cere să estimați înălțimea acestui text, ați putea spune: ” este de aproximativ 4 mm” . Folosirea cuvântului ‘aproximativ’ implică faptul că există o anumită incertitudine în estimarea dumneavoastră.
De fapt, nu putem ști niciodată valoarea adevărată exactă a ceva, toate măsurătorile sunt de fapt estimări și au o anumită incertitudine. Diferența dintre rezultatul unei măsurători și valoarea adevărată este eroarea de măsurare . Din moment ce nu putem cunoaște valoarea adevărată, nu putem cunoaște nici eroarea: acestea sunt mărimi incognoscibile.
Tot ceea ce putem cuantifica despre lumea din jurul nostru sunt rezultatele măsurătorilor, iar acestea au întotdeauna o anumită incertitudine, chiar dacă această incertitudine este foarte mică.
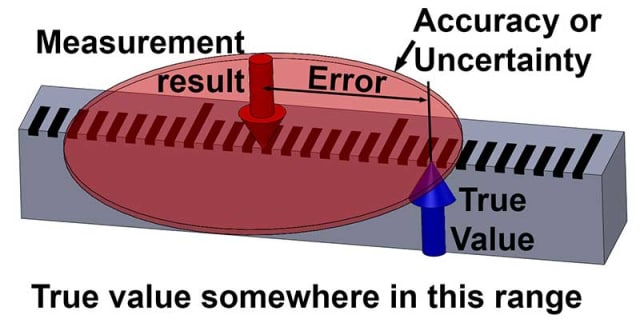
Dacă ați estima înălțimea acestui text ca fiind ‘ aproximativ 4 mm, plus sau minus 1 mm’, atunci ați atribuit acum niște limite incertitudinii dumneavoastră. Dar tot nu puteți fi 100% sigur că este adevărat.
Ați putea avea un anumit nivel de încredere, să zicem 95 la sută, că este adevărat. Dacă ar fi să măriți limitele, să zicem la aproximativ 2 mm , atunci încrederea dumneavoastră ar crește, poate la 99 la sută. Așadar, incertitudinea oferă niște limite în interiorul cărora avem un nivel de încredere că se află valoarea adevărată.
OK, ora de filozofie s-a terminat!
Într-o postare viitoare, voi dezvolta aceste idei și modul în care poate fi calculată incertitudinea pentru un anumit nivel de încredere.
Incertitudine și calitate
Odată ce am determinat incertitudinea (sau „acuratețea”) unei măsurători, o putem aplica pentru a decide dacă o piesă este conformă cu o toleranță specificată. De exemplu, să spunem că o piesă este specificată să fie de 100 mm +/- 1 mm. O măsurăm și obținem un rezultat de 100,87 mm.
Este piesa în specificație?
Răspunsul simplu este: „Nu știm, poate că este, dar poate că a existat o eroare în măsurarea noastră și de fapt piesa are mai mult de 101 mm. Poate că a existat o eroare și mai mare și piesele sunt de fapt mai mici de 99 mm!”
Dacă nu știm care este incertitudinea măsurătorii, nu avem nicio idee despre cât de încrezători putem fi că piesa se încadrează în specificații. Să presupunem că incertitudinea măsurătorii a fost dată astfel încât rezultatul măsurătorii să fie de 100,87 mm +/- 0,1 mm la un nivel de încredere de 95 %. Acum putem spune cu o încredere mai mare de 95 % că piesa se încadrează în specificații.
Așadar, înțelegerea și cuantificarea incertitudinii măsurătorilor este esențială pentru menținerea calității.
Acum, să luăm în considerare calibrarea și conceptul asociat de trasabilitate. Acesta este un aspect fundamental al incertitudinii. O calibrare este o comparație cu o referință, iar incertitudinea acestei comparații trebuie să fie întotdeauna inclusă, din motivele explicate mai jos.
O măsurătoare trasabilă este una care are un lanț neîntrerupt de etalonări care merge până la etalonul primar. În cazul măsurătorilor de lungime, etalonul primar este definiția metrului; distanța parcursă de lumină în vid în 1/299,792,458 secunde, așa cum a fost realizată de Biroul Internațional de Greutăți și Măsuri (BIPM) din Paris.
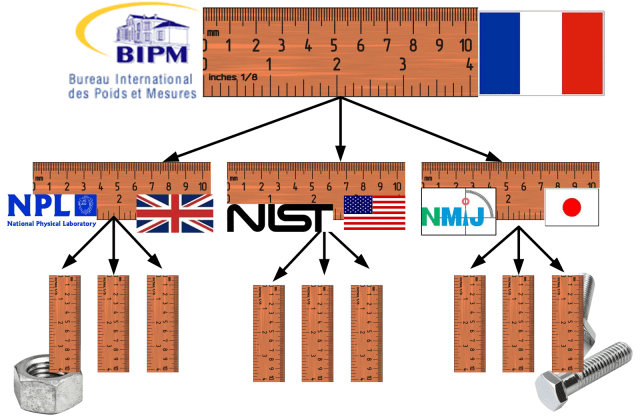
Începând cu anii 1930, inch-ul a fost definit ca fiind 25,4 mm și, prin urmare, este, de asemenea, trasabil la același standard de metru. Toate măsurătorile trebuie să fie trasabile la același standard pentru a se asigura că piesele fabricate în țări diferite se vor potrivi între ele.
Incertitudine și eroare
Incertitudinea măsurătorilor provine din diferite surse. Unele dintre acestea vor conduce la o eroare consistentă, sau la o distorsiune, în rezultat.
De exemplu, eroarea necunoscută prezentă atunci când un instrument a fost calibrat va conduce la o eroare consistentă ori de câte ori este utilizat. Acest tip de efect este cunoscut ca o incertitudine sistematică care conduce la o eroare sistematică . Alte surse vor conduce la erori care se modifică aleatoriu de fiecare dată când se face o măsurare.
De exemplu, turbulențele din aer pot provoca perturbații mici, care se schimbă aleatoriu în măsurătorile cu laser, jocul mecanic și alinierea pot provoca erori care se schimbă aleatoriu în măsurătorile mecanice. Acest tip de efect este cunoscut ca o incertitudine aleatorie care conduce la o eroare aleatorie .
Este convențional să se împartă incertitudinea aleatorie în repetabilitate , incertitudinea aleatorie a rezultatelor în aceleași condiții, și reproductibilitate , incertitudinea aleatorie în condiții modificate.
Desigur, condițiile nu pot fi niciodată exact aceleași sau complet diferite, astfel încât distincția este oarecum vagă. Tipurile de condiții care ar putea fi schimbate sunt efectuarea măsurătorii la un moment diferit, cu un operator diferit, cu un instrument diferit, folosind o calibrare diferită și într-un mediu diferit.
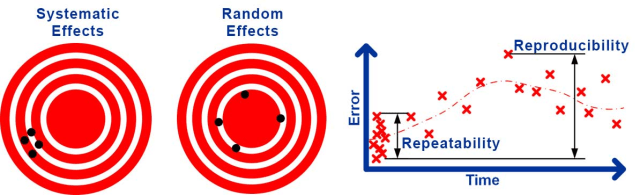
Există două metode utilizate pe scară largă pentru a cuantifica incertitudinea unei măsurători. Laboratoarele de etalonare și instituțiile științifice efectuează în mod normal evaluarea incertitudinii în conformitate cu Ghidul pentru exprimarea incertitudinii în măsurare (GUM) .
Metoda GUM implică mai întâi luarea în considerare a tuturor influențelor care ar putea afecta rezultatul măsurătorii. Apoi trebuie determinat un model matematic care să dea rezultatul măsurării în funcție de aceste mărimi de influență. Prin luarea în considerare a incertitudinii fiecărei mărimi de intrare și prin aplicarea ‘ Legii de propagare a incertitudinii ‘ se poate calcula o estimare a incertitudinii combinate a măsurării.
Abordarea GUM este uneori descrisă ca fiind de jos în sus , deoarece începe cu o analiză a fiecărei influențe individuale. Fiecare influență este în mod normal enumerată într-un tabel numit buget de incertitudine care este utilizat pentru a calcula incertitudinea combinată.
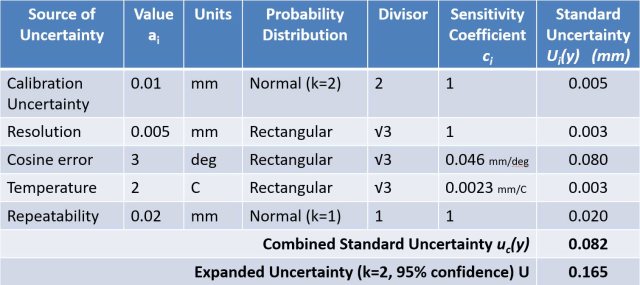
Procesele de măsurare industrială sunt de obicei evaluate utilizând o abordare de analiză a sistemelor de măsurare (MSA), așa cum se recomandă în cadrul metodologiei Six-Sigma și, de obicei, urmând liniile directoare ale Manualului de referință MSA al Grupului de acțiune al industriei auto (AIAG) .
MSA implică efectuarea de studii de măsurare în care măsurătorile repetate sunt comparate cu o referință în condiții diferite pentru a determina distorsiunea, repetabilitatea și, uneori, reproductibilitatea.
Un studiu de tip 1 este o verificare rapidă efectuată în mod normal pentru a înțelege inițial variația unui dispozitiv de măsurare. Acesta presupune ca un singur operator să măsoare o singură piesă de referință etalonată de 25 sau mai multe ori și apoi ia în considerare variația și distorsiunea rezultatelor. Acest tip de test este adesea numit studiu de repetabilitate în afara MSA.
Un studiu de repetabilitate și reproductibilitate a calibrelor (Gage R&R) este utilizat pentru a obține o înțelegere mai detaliată a unui proces de măsurare. În mod obișnuit, 10 piese sunt măsurate fiecare de două ori de cel puțin trei operatori diferiți. Se utilizează apoi o tehnică statistică numită ANOVA pentru a determina cât de multă variație este cauzată de instrument („gage”) și cât de mult este cauzată de operator. Astfel, se consideră că schimbarea operatorului și modificările ulterioare în timp și mediu reprezintă o reprezentare completă a condițiilor de reproductibilitate.
MSA este uneori menționată ca fiind de sus în jos, deoarece tratează în mare măsură procesul de măsurare ca pe o cutie neagră și determină experimental incertitudinile sistematice și aleatorii. Două concepte importante în MSA sunt acuratețea , utilizată ca echivalent al incertitudinii; și precizia , utilizată ca echivalent al incertitudinii aleatorii.
Avantajul evaluării incertitudinii este acela că este capabilă să ia în considerare toate sursele de incertitudine și, dacă este realizată corect, oferă cea mai exactă estimare a incertitudinii. Problemele acestei abordări includ faptul că necesită un metrolog capabil să producă modelul matematic și riscul de eroare umană care duce la omiterea sau estimarea incorectă a unor influențe semnificative.
Metoda GUM este, de asemenea, valabilă numai pentru o măsurare individuală care a fost efectuată cu valori cunoscute pentru orice corecții aplicate. Prin urmare, este dificil să se aplice corect evaluarea incertitudinii pentru a prezice incertitudinea unui proces industrial de măsurare.
MSA poate fi aplicată mult mai ușor și este destinată să furnizeze o predicție pentru precizia unui proces de măsurare industrială. Problema acestei abordări este că anumite efecte sistematice sunt ignorate, iar condițiile de reproductibilitate pot să nu fie pe deplin reprezentate, ceea ce duce la o subestimare a incertitudinii.
Un exemplu de omitere a efectelor sistematice este faptul că, atunci când se determină părtinirea, se face o comparație cu o referință care este tratată ca fiind valoarea adevărată – în realitate, referința are, de asemenea, incertitudine, care ar trebui inclusă. Această metodă se bazează pe faptul că toate condițiile de reproductibilitate sunt variate astfel încât efectele lor să poată fi observate în variația rezultatelor atunci când se fac măsurători repetate. Este probabil ca modul în care sunt variate aceste condiții să nu reflecte pe deplin variația observată în timpul procesului real de măsurare.
Măsurarea și asigurarea calității
Până acum, m-am axat pe controlul calității, adică pe modul în care măsurătorile pot dovedi că piesele sunt conforme cu specificațiile după ce au fost produse. Acum, să luăm în considerare pe scurt asigurarea calității, modul în care ne asigurăm că procesul produce piese bune în primul rând.
Acest aspect al calității este abordat în mare măsură de controlul statistic al proceselor (SPC) . Un proces poate fi evaluat prin realizarea mai multor piese și măsurarea lor pentru a determina variația și părtinirea în procesul de fabricație. În loc să se dea direct aceste rezultate, este normal să se împartă toleranța piesei la precizia procesului pentru a obține capacitatea mașinii-unelte ( C P ) sau la precizia procesului pentru a obține capacitatea procesului ( C PK ).
SPC este, în multe privințe, echivalent cu MSA. Acesta adoptă o abordare de sus în jos pentru a înțelege efectele aleatorii și sistematice. Cu toate acestea, în loc să evalueze măsurătorile, este utilizată pentru a evalua ieșirile procesului. În general, are aceleași avantaje și dezavantaje ca și MSA, iar o abordare ascendentă de evaluare a incertitudinii poate fi utilizată în cazul în care acestea reprezintă o preocupare.
Inițial, se poate părea că există diferențe fundamentale între MSA și SPC din cauza terminologiei foarte diferite din cadrul SPC. Cu toate acestea, variația de cauză comună (sau variația de cauză întâmplătoare în literatura mai veche) este echivalentul preciziei; variabilitatea pe termen scurt este echivalentul repetabilității; variabilitatea pe termen lung este echivalentul reproductibilității; iar variația de cauză specială (sau variația de cauză atribuibilă în literatura mai veche) este echivalentul prejudecății.
SPC pune, de asemenea, un accent mult mai mare pe asigurarea faptului că un proces se află în ‘ control statistic ‘. În termeni generali, aceasta înseamnă că efectele sunt aleatorii și normal distribuite, cu corectarea oricăror efecte sistematice semnificative. Acesta este un punct forte al SPC și este uneori trecut cu vederea atât în evaluarea incertitudinii, cât și în MSA.
Principalul instrument utilizat în SPC pentru a verifica dacă un proces este „sub control” este graficul de control . Acest lucru oferă o vizualizare grafică simplă a unui proces în care se poate observa cu ușurință când un proces este în derivă sau produce erori care nu pot fi explicate prin variații aleatorii normale. De exemplu, dacă mai multe puncte sunt toate în creștere sau în scădere, acest lucru indică faptul că procesul este în derivă.
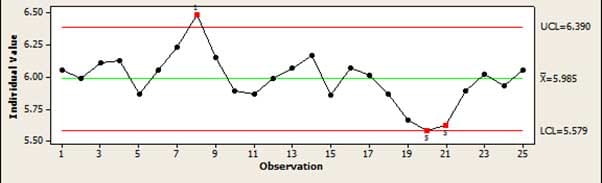
În acest articol, am încercat să ofer o privire de ansamblu asupra unui subiect vast și complex. Am introdus principiile fundamentale care stau la baza menținerii calității, fără a intra în calculele matematice necesare pentru a aplica aceste metode.
Rămâneți pe recepție pentru articolele viitoare pe aceste subiecte.
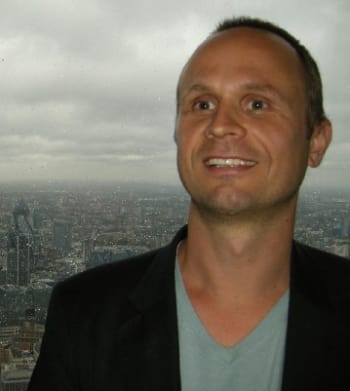
Cariera de inginer de 20 de ani a Dr. Jody Muelaner a început în domeniul proiectării de mașini, lucrând la orice, de la dispozitive medicale la mori de ferăstrău. Din 2007, el a dezvoltat metrologie nouă la Universitatea din Bath, lucrând îndeaproape cu companii aerospațiale de top. Această cercetare se concentrează în prezent pe modelarea incertitudinii sistemelor de producție, reunind elemente de SPC, MSA și metrologie cu metode numerice noi. De asemenea, este interesat de designul bicicletelor. Vizitați site-ul său web pentru mai multe informații.